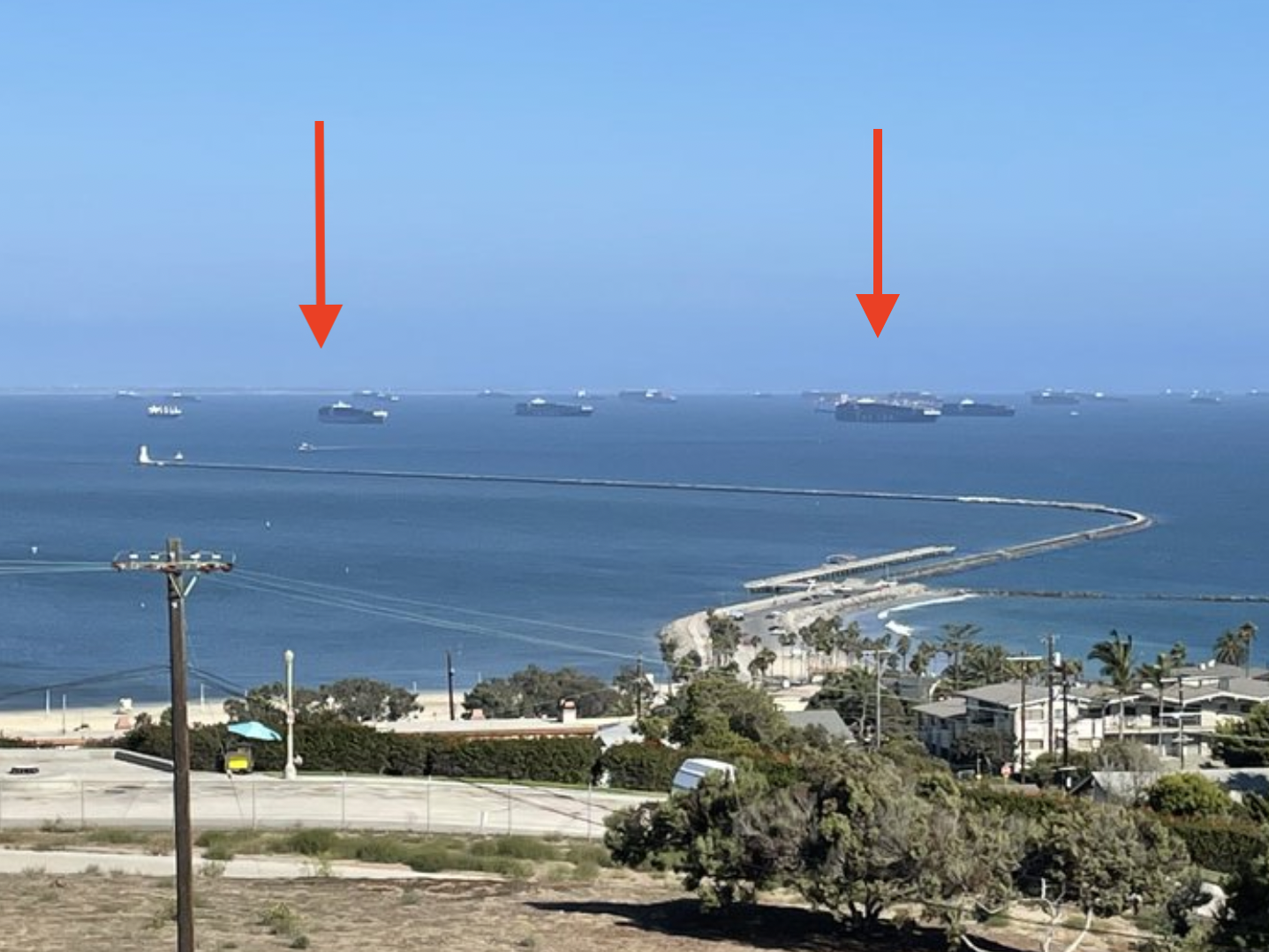
- A video breaks down how the largest ports in the US are handling record backlogs.
- Freight Right CEO Robert Khachatryan explains how the ports organize dozens of ships into "parking spots."
- The record shipping delays show no signs of abating as the holiday shopping season looms.
- See more stories on Insider's business page.
It's difficult to understand the enormity of dozens of hulking cargo ships waiting to dock along the Southern California shore unless you've seen it for yourself. A video from Freight Right Global Logistics breaks down how ports in Los Angeles and Long Beach track and organize as many as 500,000 shipping containers.
The video shows the cargo ships that wait an average of 10 days to as long as a month to dock and unload at two of the largest ports in the US. While the glut of ships may appear haphazard to the untrained eye, Freight Right CEO Robert Khachatryan explains in the video that the cargo ships have been laid out in a very specific formation designed to keep the shipping lanes clear for incoming and outgoing vessels, as well as prevent the massive ships from crashing into each other.
The Marine Exchange of Southern California, as well as the shipping companies have dashboards that continually remotely track the ships' coordinates.
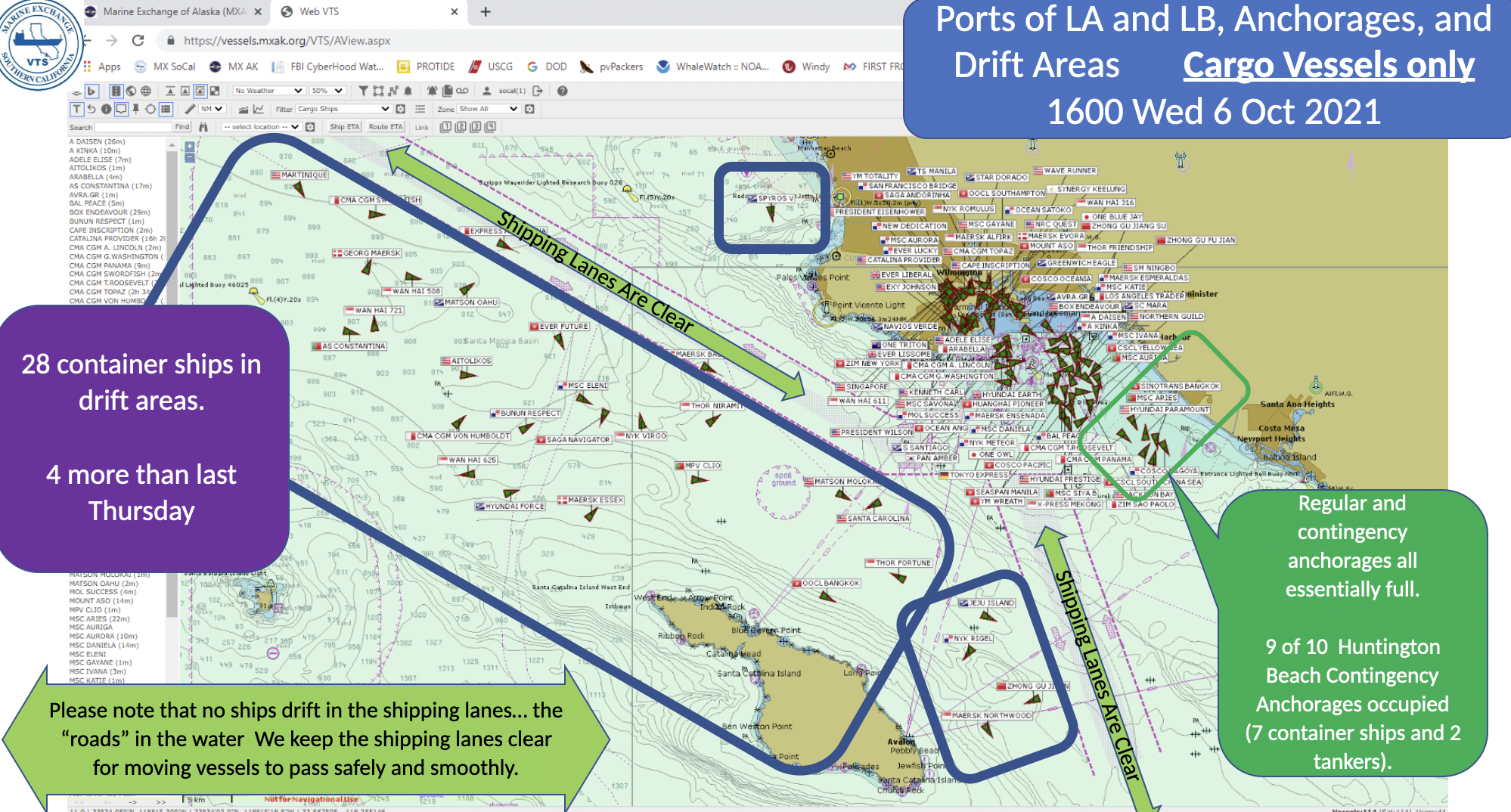
Marine Traffic of Southern California
Each vessel, whether put at drift as far as 20 miles out from the shore or parked closer at anchor, takes up numbered spots which it is assigned based on GPS coordinates.
Khachatryan said that, despite the global shortage of shipping containers, the issue is not the lack of equipment, but rather they lack of capacity for the volume of ships within the ports. He points out that the two ports, which are typically treated as one due to their proximity, can only handle about 30 ships at a time – a capacity level that would not have been an issue before COVID-19 shutdowns snarled the global supply chain.
"The port is pretty much handling all the containers it can handle given the infrastructure capacity, so adding a lot of vessels does not solve the problem," Khachatryan said in the video. "What solves the problem is moving these containers out of the port, which, unfortunately, is not happening fast enough."
As the ports face near record backlogs, the shipping companies lose more money everyday. Khachatryan said the 10-day waiting period to get into the port often causes the ships to miss out on about two voyages between Asia and the US. Many of the larger container ships waiting off the shore lose upwards of $500,000 to $600,000 everyday, according to Khachatryan.
Outside of the ships themselves, the video also shows many of the Port of Long Beach's processes, including the automated portions of the terminals where container ships are lifted by massive cranes and moved throughout the port.
The port is responsible for over 40% of US imports, but several major companies have moved to sidestep the backlog, as the average price of 20-foot shipping containers surges to record highs over $20,000.
Large companies are trying to avoid these California ports altogether. Coca-Cola recently chartered three bulk shipping vessels usually used for materials like grain and coal to charter goods to its manufacturing plants. This move was unusual for the company, citing shortages of both cargo space and shipping containers for the decision as well as a desire to avoid congested ports.
Retailers like Costco, Target, and Walmart also rented out their own container ships, reevaluating traditional methods to sidestep delays in product shipments and empty shelves in their stores ahead of the holiday shopping season.
Several other US ports have also begun to report backlogs, including ports on the East Coast, as consumer demand continues to strain an already snarled global supply chain.